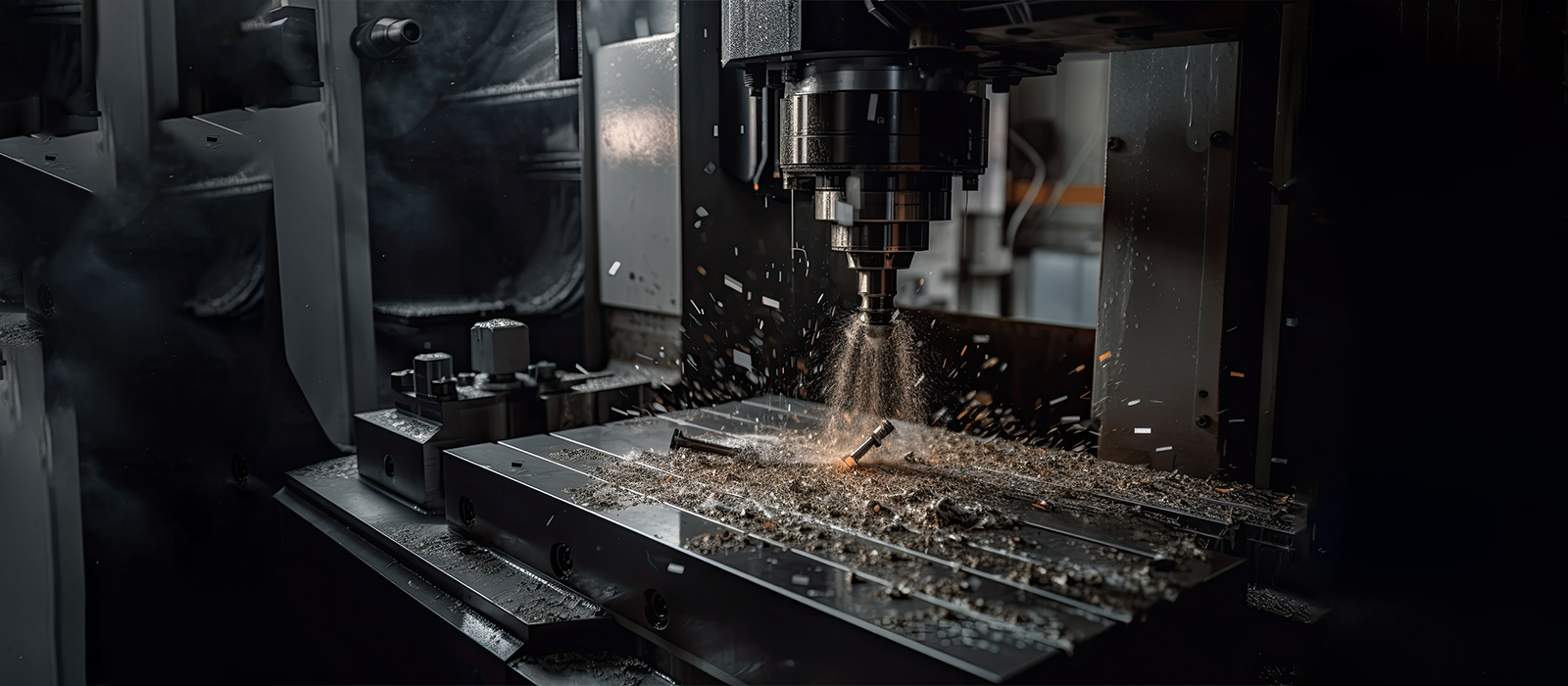
Introduction
1. High Polish Ability
Key Points:
Aesthetic Quality: Produces visually appealing plastic parts.
Smooth Surfaces: Reduces post-processing requirements.
2. Wear Resistance and Durability
Plastic mould steel offers excellent wear resistance, which is necessary for the repetitive nature
of moulding operations. This durability ensures that moulds can produce a large number of parts
without degrading, maintaining consistent quality.
Key Points:
Longevity: Extends the lifespan of moulds.
Consistent Quality: Ensures uniformity in produced parts.
3. Thermal Conductivity
Key Points:
Efficiency: Shortens production cycles
Precision: Enhances dimensional accuracy of parts.
4. Corrosion Resistance
Key Points:
Protection: Prevents mould degradation from corrosion
Lightweight Options: Improve efficiency in construction and machinery.
5. Applications in Modern Manufacturing
Injection Moulding: Producing parts for automotive, electronics, and consumer goods.
Blow Moulding: Creating hollow plastic products like bottles and containers.
Compression Moulding: Used for high-strength, durable plastic components.
Key Points:
Versatility: Suitable for various moulding techniques.
Precision: Essential for high-quality plastic manufacturing
Conclusion
How Plastic Mould Steel Enhances Modern Manufacturing
The Importance of Plastic Mould Steel in Manufacturing
This plays a vital role in modern manufacturing processes, offering essential properties that enhance the production of high-quality plastic parts.
High Polish Ability of Plastic Mould Steel
Achieving Superior Aesthetic Plastic Mould steel Quality
it's ability to achieve a high polish is crucial for producing visually appealing plastic components, especially for consumer products.
Wear Resistance and Durability
Extending the Lifespan
The excellent wear resistance of steel ensures that moulds last longer, maintaining their quality over numerous production cycles.
Add a Comment